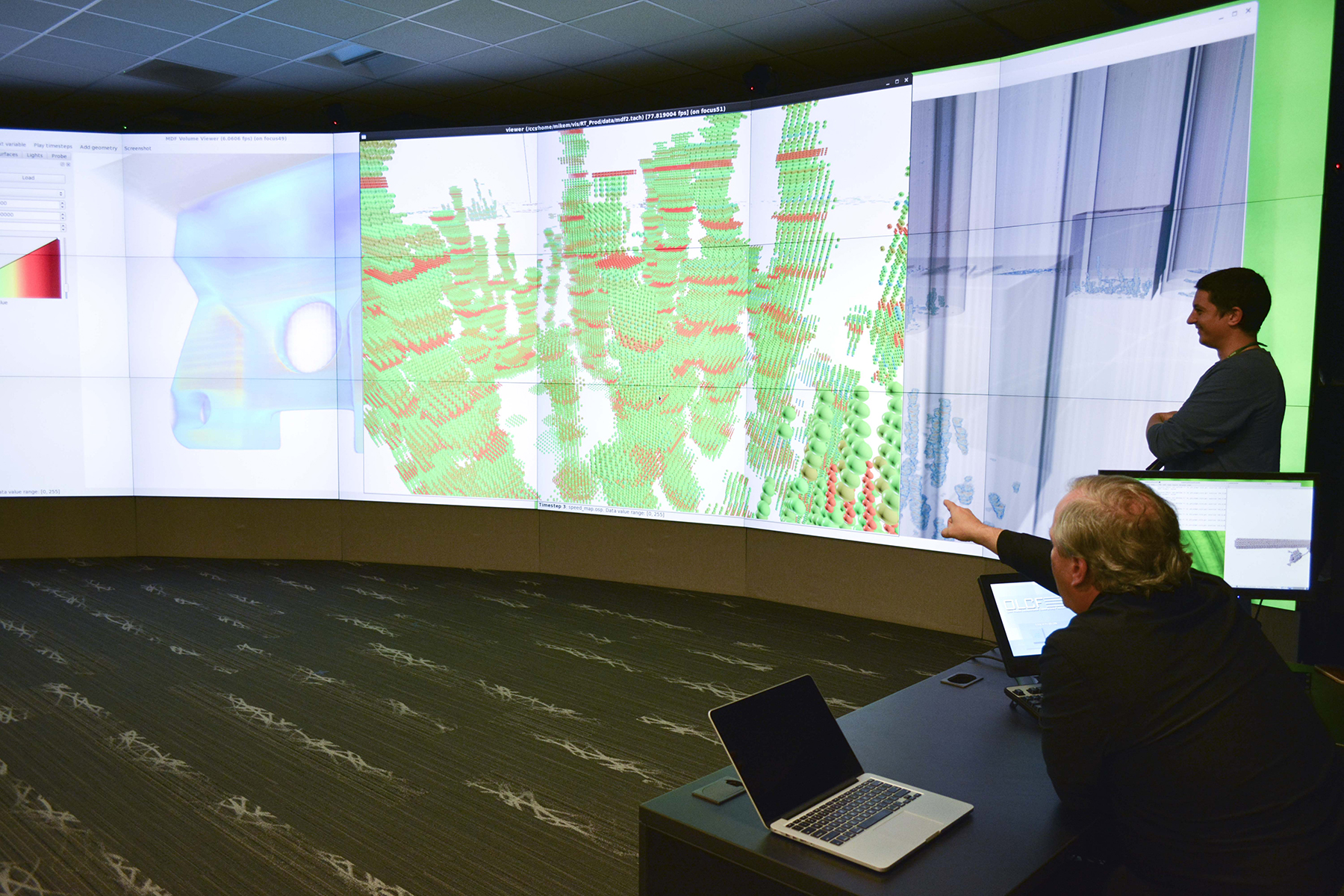
Mike Matheson (front), an Advanced Data and Workflow group member and primary developer for a new visualization workflow, and Vincent Paquit (back), an R&D scientist at the MDF, demonstrate 3-D visualization and real-time rendering of additive manufacturing data on EVEREST.
New workflow helps improve visualization and production
Additive manufacturing (AM)—commonly known as 3-D printing—is transforming the manufacturing industry by allowing the design and development of highly complex objects that would be impossible to create with traditional manufacturing methods.
AM is now at the tipping point of being broadly adopted by the industry as a new standard for manufacturing. At this point, the missing piece to the puzzle is certification and validation—in a nutshell, ensuring that printed objects are within their geometric design specifications and have the material properties required for their final use.
To advance this technology and to address the certification requirements in particular, the US Department of Energy (DOE) has made strategic investments at the Manufacturing Demonstration Facility (MDF) toward the development of a Data Analytics Framework for Manufacturing. By integrating scientific knowledge from teams of researchers focusing on material development, method optimizations, and data analytics, this framework aims to provide a better understanding of the material properties obtained under varying additive manufacturing conditions and parameters.
For materials scientists, the ability to visualize this information in 3-D is crucial because it provides new insight on object quality and spatial information correlation. For this task, the MDF—located at DOE’s Oak Ridge National Laboratory (ORNL)—reached out to the Oak Ridge Leadership Computing Facility’s (OLCF’s) Advanced Data and Workflow Group. The OLCF is a DOE Office of Science User Facility.
The project began last fall after MDF staff realized the need for access to high-performance computing resources and visualization expertise to study variables related to additive manufacturing at a terabyte scale with extremely high resolution.
“We have experts who can help us do this at ORNL, so it made perfect sense to reach out to the Advanced Data and Workflow Group and leverage its expertise in the field,” said Vincent Paquit, an R&D scientist at the MDF. “We can gain greater understanding of the manufacturing process just by visualizing the data and manipulating the variables—something that the group is great at.”
Testing 3-D printed objects begins with building the same part with several different parameters. The printing process itself can produce defects such as porosities—gaps in the material structure that can lead to part failure under stress from normal use. It is important for researchers at the MDF to understand what printing parameters lead to these defects and which processes work best for ensuring quality products.
“Currently, 3-D printing is at a stage where it’s not mature enough to have set parameters that guarantee a product with no defects,” said Sreenivas Rangan Sukumar, group leader for the Advanced Data and Workflow Group. “By visualizing the object, the MDF can determine what is and isn’t causing the defects.”
To study its printed objects, the MDF requires high-quality images generated at interactive frame rates on large datasets containing many variables. Off-the-shelf visualization tools are unable to handle such demands, but the OLCF’s EVEREST, with custom software and the necessary compute systems, is capable of providing this high level of performance.
“When people think about EVEREST, they often think of a giant screen, but they don’t appreciate the entire design of I/O, memory, computational power, and graphic power that’s necessary to do difficult problems,” said Mike Matheson of the Advanced Data and Workflow Group.
The visualization workflow that Sukumar’s group developed pulls data in real time from the MDF to the OLCF, a DOE Office of Science User Facility located at ORNL. This data includes input data from the computer-aided design model, in situ and ex situ image data, and immediate measurements from the printer. The data can then be recalled by EVEREST so MDF staff can visually determine how printing parameters and processes influence the printed component’s porosity, malleability, and other structural characteristics, according to Matheson, the primary workflow developer.
Currently, the MDF is the main user of this workflow. However, after additional OLCF users expressed interest in using 3-D visualization, Sukumar’s group began working to expand the service.
“The visualizations developed by OLCF users don’t often exist in the real world,” Sukumar said. “We can’t see plasma or the entire universe. We can’t see water molecules or the airflow surrounding semi-trucks. What if we could print these? We could give space and time to phenomena that you don’t typically see or feel or work with.”
Moving forward, OLCF’s ADW group plans to develop a mechanism that allows the MDF to view its 3-D artifacts remotely. MDF staff will be able to wear a virtual reality headset called Oculus Rift and walk through the 3-D models from anywhere.
By helping to ensure products get certified for quality, the visualization work is moving 3-D printing one step closer to transforming how high-quality commercial parts are made.
Oak Ridge National Laboratory is supported by the US Department of Energy’s Office of Science. The single largest supporter of basic research in the physical sciences in the United States, the Office of Science is working to address some of the most pressing challenges of our time. For more information, please visit science.energy.gov.