Simulations performed on the Cray XK7 Titan supercomputer at the Oak Ridge Leadership Computing Facility (OLCF) filled in a knowledge gap about high-temperature–capable alloys and inspired engineers to successfully develop a new cast aluminum–copper alloy that promises to withstand engine temperatures as high as 300°C—a temperature too extreme for current aluminum alloys—and offer more design flexibility.
The collaborative project involved an exploration of the mechanisms behind the stabilization of high-temperature–capable alloys and included engineers and researchers from the US Department of Energy’s (DOE’s) Oak Ridge National Laboratory (ORNL), North American automaker FCA US LLC, and casting manufacturer Nemak.
The collaborators completed the project in less than 4 years—an unprecedented amount of time for such a feat, considering most automotive engines have employed the same alloys for decades because of the tedious nature of alloy development. DOE’s Energy Efficiency and Renewable Energy Office funded the project through a cooperative research and development agreement (CRADA).
Although current cast aluminum alloys can reach peak temperatures of 250°C, they experience a rapid decrease in their mechanical properties at higher temperatures. Therefore, the team decided to explore aluminum–copper alloy strengthening and stability mechanisms to discover how to expand the operating temperature range of cast aluminum.
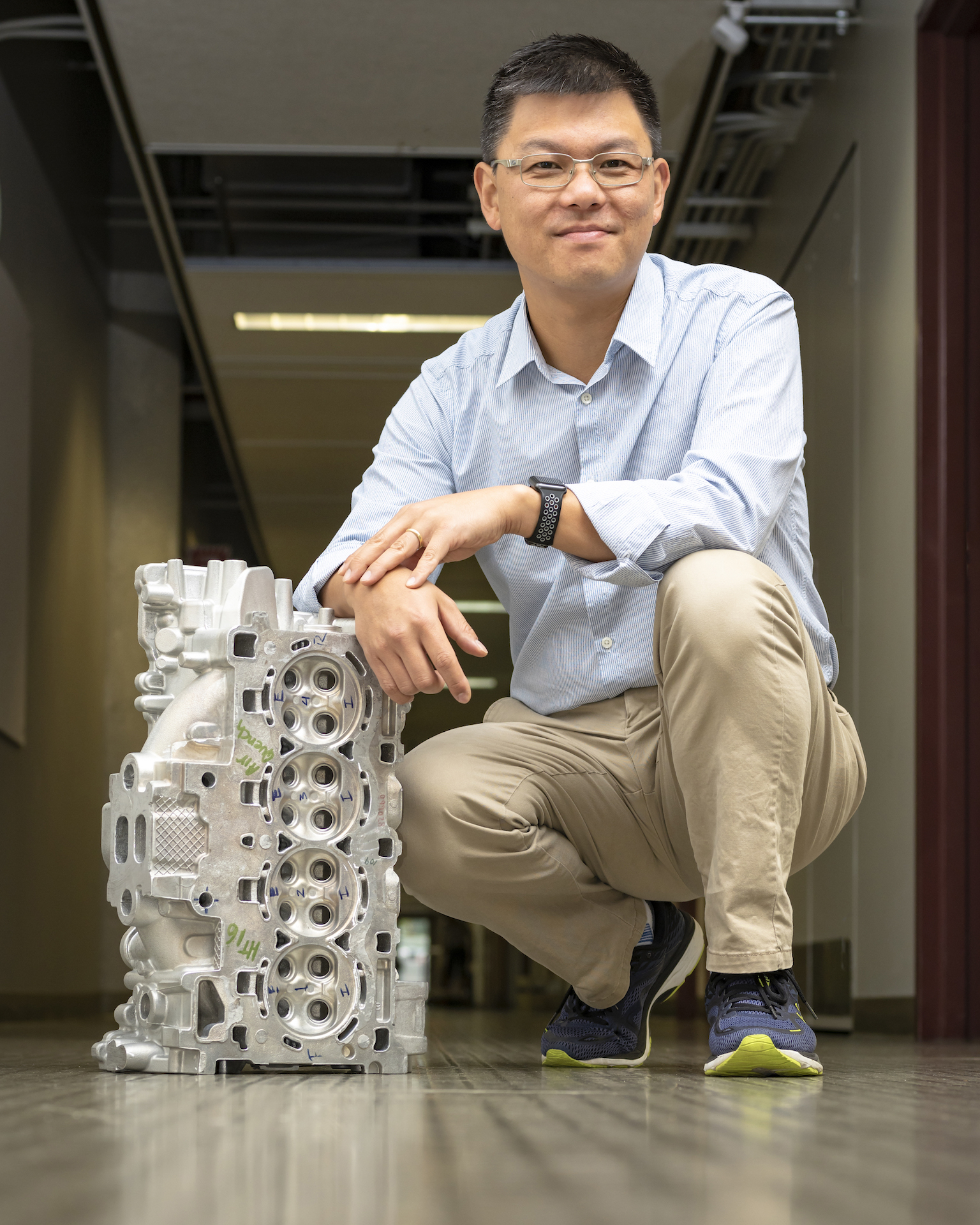
Dongwon Shin performed simulations on Titan to explore the mechanisms that make some aluminum–copper alloys thermally stable at high temperatures. Image Credit: Carlos Jones, ORNL
Early in the project, Dongwon Shin of the ORNL Materials Processing and Joining Group performed simulations on Titan at the OLCF, a DOE Office of Science User Facility at ORNL. The goal was explaining the team’s key microstructural observations: the unusual size and stability of strengthening precipitates in a cast aluminum–copper–nickel alloy from the World War II era. The computational simulations of these unusual microstructures explained the mechanisms by which some aluminum–copper alloys are able to retain their strength at higher temperatures.
Shin used the Vienna Ab Initio Simulation Package—a quantum mechanics code—to perform “supercell” simulations of the thermodynamics at play when element combinations are thermally stable. He specifically looked at the reactions occurring at the interface between a strengthening precipitate formed in the heating process and the surrounding metal in the alloy. He found that certain solute elements, particularly manganese and zirconium, can stabilize the high-energy interface of the two and prevent the reactions from rapidly growing out of control and weakening the alloy.
This virtual experiment required several hundred supercell simulations and would have taken several months elsewhere, but Shin finished it in a couple of weeks, thanks to Titan’s accelerated architecture and the OLCF’s unique queueing policy. Instead of running several hundred supercell simulations in serial, Shin created a large ensemble job that enabled massive parallelization using a significant amount of Titan’s nodes.
The team then leveraged these experimental and computational discoveries into the design of a new family of alloys that were not only more durable at higher temperatures but also more castable and more affordable than the aluminum–copper–nickel alloys.
“Alloys that can withstand these higher temperatures are typically pretty expensive and difficult to cast,” Shin said. “This alloy family is not only highly castable, but we also don’t need to use expensive elements like nickel and cobalt in our ‘recipe.’”
The CRADA team, led by Amit Shyam of ORNL’s Alloy Behavior and Design Group, considered 50 new aluminum–copper alloys based on the findings. FCA and Nemak engineers then worked with the experimentalists at ORNL to narrow the results to seven high-potential alloys that are part of a family called the aluminum–copper–manganese–zirconium (ACMZ) alloys.
One of the major differences among alloys is the primary strengthening component—typically either silicon or copper. Traditional cast aluminum–copper alloys can be expensive to process because they are prone to cracking during casting. Aluminum–silicon alloys do not have this problem and thus are more common today. The researchers found, however, that the ACMZ alloys cast as well as some of the aluminum–silicon alloys and better than the traditional cast aluminum–copper alloys.
FCA and Nemak have cast more than 100 production-scale cylinder heads from various ACMZ alloys. One ACMZ alloy composition, also known as 16HT, underwent FCA’s most rigorous 500-hour proof-of-concept engine test via a dynamometer—which measures an engine’s power production—in December 2017 at FCA.
The team is hopeful that the new family of ACMZ alloys will allow engineers to produce lightweight, temperature-resistant cylinder heads offering more flexibility in future advanced engine designs.
“It will certainly be a few years before we see the alloys in a production engine,” Shyam said. “There is still development work that needs to be done and additional tests that FCA needs to run, but the progress we’ve made so far is very promising.”
Shyam’s team is currently exploring how to further apply computational simulations to new alloy development in addition to extending its alloy studies to aim for even higher temperatures.
“This is really complicated,” Shin said. “We have so many different element combinations and so many different phases that we’re looking at, and we have to understand the thermodynamics and kinetics of all these different interactions. This is a great challenge, but the OLCF gives us new capabilities to solve these kinds of problems.”
The team won an R&D 100 Award in 2017 for the ACMZ alloys breakthrough and was honored at the 55th annual R&D 100 Conference, sponsored by R&D Magazine.
In addition to Shin and Shyam, team members on the project include ORNL’s J. Allen Haynes, Yukinori Yamamoto, Adrian Sabau, Lawrence Allard, Thomas Watkins, Wallace Porter, James Morris, Shibayan Roy, Philip Maziasz, Dana McClurg, Charles Hawkins, Patrick Shower, and Brian Milligan; Fiat Chrysler’s Gregg Black, Chris Glaspie, Seyed Mirmiran, Yi Liu, and Lin Zhang; and Nemak’s Andres Fernando, Jose Talamantes, and Jose Alejandro Gonzalez.
Related Publications: Dongwon Shin, Sangkeun Lee, Amit Shyam, and J. Allen Haynes, “Petascale Supercomputing to Accelerate the Design of High-Temperature Alloys,” Science and Technology of Advanced Materials 18, no. 1 (2017): 828–38, doi:10.1080/14686996.2017.1371559.
Dongwon Shin, Amit Shyam, Sangkeun Lee, Yukinori Yamamoto, and J. Allen Haynes, “Solute Segregation at the Al/θ′–Al2Cu Interface in Al–Cu Alloys,” Acta Materialia 141 (2017): 327–340, doi:10.1016/j.actamat.2017.09.020.
ORNL is managed by UT-Battelle for the Department of Energy’s Office of Science, the single largest supporter of basic research in the physical sciences in the United States. DOE’s Office of Science is working to address some of the most pressing challenges of our time. For more information, please visit https://science.energy.gov.