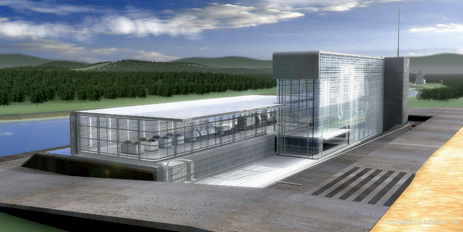
An artist’s rendition depicts the goal of the FutureGen initiative, which aims to build the world’s first integrated sequestration and hydrogen production research power plant based on coal gasification. Source: DOE Office of Fossil Energy
Next-generation plants to produce electricity and hydrogen and sequester carbon dioxide Near-zero-emission coal plants are in the works to generate electricity and hydrogen and sequester carbon dioxide. Using high performance computers at the National Center for Computational Sciences, DOE researchers simulate coal gasification processes to help industry develop efficient plant designs.
In prehistoric times, plants died in swamps and water thwarted their oxidization. Over time, geological processes pressurized and mineralized the plants, which turned to coal. Today, Department of Energy (DOE) researchers at the National Energy Technology Laboratory (NETL) and Oak Ridge National Laboratory (ORNL) are using supercomputers to improve the industrial design of facilities that tap coal’s oxidative potential while trapping its pollutants.
“An important part of NETL’s mission is to supply clean coal technology, and our research group at NETL develops computational tools and applications in support of that mission,” says principal investigator Madhava Syamlal of NETL. With Chris Guenther (NETL), Aytekin Gel (Aeolus Research Inc./NETL), Phil Nicoletti (Parsons/NETL), and Sreekanth Pannala (ORNL), he uses the Cray XT4 Jaguar supercomputer at DOE’s National Center for Computational Sciences (NCCS) to simulate coal gasification processes. The highest-resolution coal-gasification simulation to date should enable faster development of clean coal technology.
The research contributes to clean coal technology projects using advanced power generation technologies such as Integrated Gasification Combined Cycle, or IGCC. Next-generation IGCC plants are envisioned that emit nearly no nitrogen oxide, mercury or sulfur and that trap most carbon dioxide.
In gasification, coal is pulverized and partially oxidized to separate fuel-rich hydrocarbons from pollutants. Coal solids are recycled through the system until they are completely gasified to produce “syngas,” a mixture of hydrogen and carbon monoxide. The syngas can be used to produce hydrogen or to generate electricity (for example, using gas turbines) in a clean and efficient manner.
“The United States has more than 200 years of mineable coal reserves at current consumption rates,” says Pannala. “Coal is also an integral part of the world’s energy mix and is especially a source of energy in the rapidly developing economies of India and China. This research will benefit the world through development of clean coal technologies.”
The United States is home to 27 percent of the world’s coal reserves, followed by Russia (17 percent), China (13 percent), and India (10 percent). The combustible mineral meets one-quarter of the world’s energy demands. About 80 percent of China’s and 50 percent of America’s electricity come from burning coal.
President Bush pledged $2 billion over 10 years to advance clean coal technology under his Clean Coal Power Initiative, which will help utilities meet the President’s Clear Skies Initiative to cut sulfur, nitrogen, and mercury pollutants from power plants by nearly 70 percent by the year 2018.
The motivation for investment to accelerate high-risk, high-rewards research is clear, Pannala says. Unless the production of hydrogen and electricity from coal, integrated with sequestration of carbon dioxide, is shown to be feasible and cost-effective, the industry will not make investments needed to fully achieve the energy and economic benefits of coal.
In the mid-1990s, industry and government collaborated to build coal gasification research and development test facilities to design advanced technologies. In response to supercomputer simulations, engineers adjust operating conditions to learn what works best.
“Essentially, we’re trying to get the highest-resolution data to date for coal gasification to feed into these test facilities,” Guenther says. “For example, it’s critical to understand the impact inlet ports for coal have on the gasification process. Inlets are important and are a challenging area of research because of the complex mixing, chemistry, and temperature gradients that exist in these areas. Correctly capturing inlet regions is critical in our simulations, not only to understand local conditions in these areas, but also to understand how injection of coal can impact the conversion of coal into syngas.”
To examine injection ports in detail, the NETL researchers will run simulation on Jaguar for two weeks in January 2008 that will provide 1 millimeter resolution. Jaguar’s high resolution, represented by computational cells, means combustion can be modeled in great detail, enabling simulations that represent reality with unprecedented fidelity. Jaguar’s enormous memory and speed produce quicker answers to scientific and engineering questions and accelerate development of the technology.
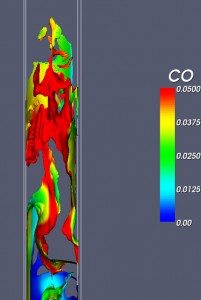
Efficient gasifiers maximize carbon monoxide (CO) production. Particle clusters colored by CO concentration are shown. Image courtesy: National Energy Technology Laboratory.
An open-source software code developed at NETL runs the simulation. Called MFIX, for Multiphase Flow with Interphase Exchanges, the code describes the hydrodynamics, heat transfer, and chemical reactions in fluid-solids systems. Its latest version was selected as one of the top 100 technologies of 2007 by R&D Magazine. The team made changes to MFIX to scale the code to work on 2,048 of Jaguar’s processors—a 50-fold increase in the number of processors used over previous simulations. The changes improved the parallel efficiency of MFIX by a factor of three and enabled gasifier simulations using 10 million computational cells.
“There’s a move toward modeling instead of building expensive prototypes,” says Ramanan Sankaran, an NCCS liaison who optimizes code so researchers can wrest the most science from the supercomputers. Guiding the design process through simulation rather than trial-and error speeds the development of an experimental prototype that works, he says. “Once that prototype is built, researchers can run different experiments and get a new answer every hour.”
This work was funded by the DOE Office of Fossil Energy; computer time was provided by the DOE Office of Science.