Researchers simulate the design of next-generation turbines
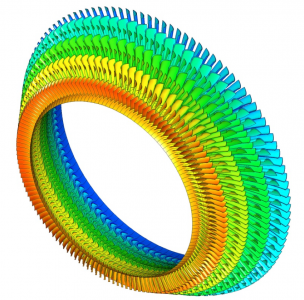
A visualization of a 4-stage low-pressure turbine modeled on the Jaguar supercomputer. With their flagship code known as Tacoma, GE ran their largest ever computational fluid dynamics simulation on Jaguar. Image courtesy GE Global Research.
Few technologies are more vital to modern day life than turbomachines, the bladed devices used to convert fluid power to and from mechanical power to drive propellers, wind turbines, gas turbines, steam turbines, fans, and compressors. These engineering marvels are literally responsible for keeping the lights on given most of the world’s electricity is generated by various kinds of turbines. And jets couldn’t stay aloft without them to drive a plane’s large-diameter fans.
General Electric (GE), the iconic technology, service, and finance company and American industrial leader, has been building turbomachines for nearly a century and is currently a major producer for the electric power generation and aircraft engine industries. Recently, however, GE took its turbomachinery research and development to the fast lane with the help of one of the fastest computers in the world.
Due to the amount of research invested in today’s turbomachinery and the sophisticated nature of its engineering, companies have repeatedly grabbed the low-hanging fruit to achieve increased efficiencies, and competition is quite fierce.
“It’s a very competitive business,” said Principal Engineer Graham Holmes of GE Global Research, noting that the company is up against Rolls Royce and Pratt & Whitney in the aviation market and Siemens and Alstom in the power generation arena. “If you could achieve a 1 percent increase in efficiency for a turbomachine, the market would be yours.” That 1 percent fuel-burning advantage would, over time, add up to enormous energy and cost savings for GE’s customers and provide GE with a business-critical advantage, according to Holmes.
Enter Jaguar, the Department of Energy’s (DOE’s) flagship Cray XT5 high-performance computing (HPC) system, located at Oak Ridge National Laboratory (ORNL). Through ORNL’s HPC Industrial Partnerships Program, GE recently harnessed Jaguar’s power to study the unsteady fluid flows in turbomachines in greater detail than ever before accomplished. Understanding these flows is essential to achieving greater efficiency and for GE to gain an edge in an intensely competitive global marketplace.
It’s all in the blades
The basic physics of turbomachinery operations have been well understood for years—jet engines and gas turbines go back to the mid-twentieth century. Essentially, turbomachines feature alternating rows of stationary and moving blades either expanding or compressing gas. The design process has evolved from experimentation and highly simplified analytical models to increasingly sophisticated simulations carried out on increasingly powerful computers. Engineers typically shape blades, run a combination of simulations and experiments, tweak the design, and repeat, which is an expensive path to production by any measure. GE runs these simulations on its in-house Linux clusters. But even with these systems, turbomachinery designers have had to assume that the velocity of air around and across the blades remains steady in the reference frame of the blades, or as seen from the point-of-view of the actual blades.
Turbomachinery designers have always understood that this air flow is unsteady and that it has to be unsteady for a turbomachine to work. But the assumption that the flow, as seen by each blade row, can be approximated as steady has proven to be remarkably powerful. The designs of all the most efficient turbomachines, such as the turbines that drive the large-diameter fans in modern jet engines, have been created using this paradigm.
Any future efficiency improvements will likely depend on deciphering the unsteady nature of the fluid flow. For example, in jet engines low-pressure turbines drive increasingly larger diameter fans, rotating at lower revolutions per minute to increase efficiency. But running low-pressure turbines at lower speeds presents a severe technical challenge—the lower the relative velocity between the blade rows, the harder it is to extract energy to drive the fan, requiring more rows of blades. Unfortunately, as more rows of blades are added, the turbine becomes heavier and therefore less efficient. Understanding the unsteady flows should allow designers to make needed adjustments without adding to the weight of the turbine, resulting in overall greater fuel efficiency.
Unsteady flow analysis is also essential to understanding other phenomenon like blade flutter, or the blade vibration induced by the fluid flow. Blade flutter can be catastrophic in an aircraft engine if it results in damage to one or more blades and turbine failure.
Ready to ramp up
GE was eager to compare its longstanding steady flow assumptions with actual unsteady flow calculations, but this posed a major computational challenge. Unsteady simulations are orders of magnitude more complex than simulations of steady flows and beyond the capability of GE’s Linux clusters. So GE applied for and received access to Jaguar, DOE’s most powerful supercomputer and one of the most powerful in the world.
Holmes was joined by Branden Moore of GE Global Research’s Advanced Computing Lab to make the most of this opportunity. They further expanded the collaboration with senior engineer Stuart Connell on the visualization front to better decode the mountain of data being produced in action.
“We definitely have the benefit of cross-discipline work at GE,” said Moore, adding that this collaborative nature ultimately helps GE’s HPC applications run faster. And running faster is a key metric in HPC. The faster a code runs, the more simulations that can be run in a given timeframe. And more simulations increase the opportunity for new insights and new scientific discovery. GE used its flagship code Tacoma, which features specialized computational fluid dynamics (CFD) for turbomachinery. When they paired Tacoma with Jaguar, GE researchers ran their largest-ever CFD calculation and were able to investigate for the first time the unsteady flows in turbomachinery. Simulations were then ramped up from three to four dimensions, and researchers were able to look at the time-resolved unsteady flows in the moving blades.
Ultimately, said Holmes, GE’s goal is to make better machines. The suite of simulations, which will benefit GE Aviation and GE Energy, was “an attempt to explore a better way of analyzing flow in those machines,” he said. “Designers want to know how to shape the blades in a turbine to improve performance. With Jaguar our team did just that, investigating various blade interactions and the unsteady flow around them to see how the overall machine performed.”
Tomorrow’s turbine
With access to Jaguar, the team was able to examine a turbine test rig and compare steady and unsteady flows. In the two analyses, the efficiency remained the same, which is “an extremely valuable piece of information,” said Holmes. Furthermore, the team found plenty of interesting unsteady phenomena occurring throughout the device. For instance, the interactions between the blade and hub created unsteady secondary flows, which behaved differently than those witnessed in the steady analysis.
The team does not yet know why the secondary flows appear unique, but they definitely want to, said Holmes. “We need to dig in and use this information to improve our visualization skills,” he said, adding that the team needs to develop a deeper comprehension of the differences in flows and decipher whether the environment or various test factors are to blame. After all, in a global industry chasing a 1 percent increase in efficiency, every little bit counts.
Overall, said Holmes and Moore, GE’s simulations on Jaguar advanced the company’s R&D in the turbomachinery arena and are providing it with a distinct competitive advantage as the company pores over the simulation results.
The team believes that GE and its competitors will move farther into unsteady flow analysis to achieve the final point in efficiency, a move that will require substantial HPC resources. In fact, largely as a result of these calculations, GE recently purchased its own Cray system, a move that significantly ramps up its in-house HPC capability.
According to Holmes, “we simply could not design a competitive turbine or jet engine without these CFD tools. We would have exited the business a long time ago on both aviation and power generation.”